VOL.22
2025.08
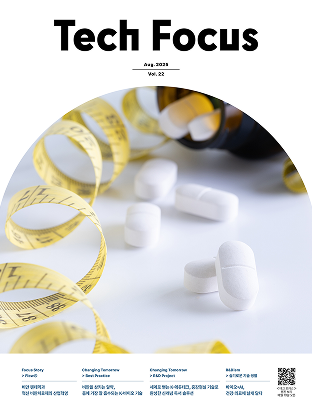
GLP-1 계열 비만치료제의 인기가 나날이 높아지고 있다.
대표 격 제품인 위고비Wegovy는 일론 머스크, 오프라
윈프리 등 세계적인 유명 인사들이 감량 효과를 실제 경험했다고 알려지며 품절 사태를 겪기도 했다.
이러한 흐름에 따라
글로벌 제약사들은 GLP-1 계열의 비만 치료
주사제를 연이어 출시하고 있다. 동시에 다음 단계,
즉 ‘먹는’ 비만치료제 개발에 주력 중이다.
연구과제명
바이콘테크 기반 단백질 약물의 경구투여 제품화 기술 개발
제품명(적용 제품)
MET-002o(DD02S)
개발기간
(정부과제 수행기간)
2020.07.01~2025.03.31.
총 정부출연금
45억6100만 원
개발 기관
㈜디앤디파마텍
참여 연구진
이슬기, 임성묵, 박은지, 신재희, 전옥철, 진주현, 윤진호, 최수영, 김남희, 우수민, 오명진, 양혜경, 이환희, 최지영, 김다애